Granulator
High quality high output hot plastic pellet/pipe/cubeextruder machine plastic recycling equipment
SJ series single screw extruder plastic machine mainly apply to extrude PP,PE,PET,PVC,ABS,PS,PA ect material.It adopt special gear box,and has features of low noisy ,stable running ,high carrying capacity,long service life .Equipped with different mold and auxiliary equipments, it could produce plastic pipe ,sheet ,board, granules and so on .It has features of simple process,high output ,stable extrusion pressure,and low cost.
Project: DJ85 single screw pelletizing line |
Raw material & formula |
PE films |
Final product |
PE granules |
Output capacity |
120-200kg/h , depends on material’s characteristics. |
Central height |
1.14m |
pp pe pelletizing line plastic recycling granulating machine waste plastic granules making machine
Parameters(CS Series Double Stage Compactor-Granulator):
Model(double stage)
|
CS85-100
|
CS100-120
|
CS130-150
|
CS160-180
|
CS180-200
|
Screw Diameter(mm)
|
85
|
100
|
130
|
160
|
180
|
L/D
|
25-42
|
25-42
|
25-33
|
25-33
|
25-33
|
Capacity(kg/h)
|
150-200
|
300-350
|
500
|
600-700
|
800-1000
|
Application:
PE, PP film, Silk, Flakes (≤0.5mm), Bags, etc.
Note, our CS series compactor granulator can be pull strip cutting method, or water ring cutting method for option
Consist of:
Belt conveyor(metal detector) → Compactor → Main extruder(vacuum degassing system) → Hydraulic screen changer → Sub- extruder →
Hydraulic screen changer → Water ring cutting system →Dewatering machine → Air blow system → Storage hopper → control cabinet
1. General information
1.1 Floor space
Basic construction, earthwork, wall work should be well finished by Buyer for accepting this pelletizing line.
Buyer should supply crane, forklift or other lifting equipment, mounting materials and tools.
Area: to be designed according to line layout.
1.2 Power supply
Installed power: 106KW (practical power consumption will be approx. 70%)
Power supply:
Supply voltage: 3*380V+N+PE;
Voltage tolerance: +10%/-5%;
Control voltage: 24VDC+220VAC;
Frequency: 50Hz+-2%
Wire/cables:
- Wires/cables from power supply to control cabinet (provide by Buyer).
- All electrical cables from control cabinet to each machine (provide by Buyer).
1.3 Water supply
Consumption: 0.6T/h (water recycles)
Cooling water:
Without dissolved or suspended minerals as phosphor, sulphur, iron, etc.
Inflow temperature T1: max. 15℃
Outflow temperature T2: T2=T1+5℃
Inflow pressure, min: 2.5 bars
Hardness: 5-8ºdH;
Reflux: without pressure
Water hose:
From water supply to every single machine (provided by Buyer).
1.4 Compressed air: 0.6M3/min, 0.4~0.7Mpa
1.5 Operation staff
2-3 People
1.6 Lubrication oil
Acquired in the local market on the recommendation of Seller (provide by Buyer).
2. Commercial terms
2. 1Machine list & Price
No.
|
Device Name
|
Model
|
Qty(set)
|
1
|
Belt conveyor
|
|
1
|
2
|
Compactor
|
|
1
|
3
|
DJ85/33 single screw extruder
|
DJ85/33
|
1
|
4
|
Plate type Hydraulic screen changer160
|
|
1
|
5
|
Water ring cutting system
|
|
1
|
6
|
Vibrating screen dewatering machine
|
|
1
|
7
|
Silo
|
|
1
|
8
|
Electric cabinet
|
|
1
|
2.2 Payment terms
- 40% as deposit by T/T.
- 60% as balance by T/T before delivery and after inspection.
2.3 Delivery time
In 50 working days from the date of receiving deposit.
2.4 Packing
Plastic film.
2.5 Warranty
13 months for mechanical parts from date of bill of lading. Three months guarantee for electric elements if power supply in Buyer’s factory is not stable.
cuishi will charge the Buyer cost price of spare parts after the equipment out of warranty and provide long-term technical guide.
2.6 Installation & Commissioning
- Buyer should get prepared for installation when the equipment arrived, such as power supply, water supply, labors and cranes, etc.
- cuishi will prepare for visa application for the engineers, who will go to Buyer’s factory for commissioning job.
- Buyer should afford round-trip air tickets for the engineers if visa application is approved, and bear expenses generated such as visa formalities, meals, accommodation and allowance of USD100 per day for each engineer.
2.7 Validity
- 60 days from quotation date.
3. Technical specification
3.1DJ85 Single screw extruder
1 |
Belt conveyor |
|
As a standardized design, plastic wastes such as film, silk, rope, bags, non-woven fabrics are conveyed into the compaction bin of the cuishi system through the belt feeding device. The conveying speed of the belt feeding device is linked with the fullness of the compaction bin, and the conveying speed of the waste material is automatically adjusted according to the fullness of the compaction bin.Motor power: 1.5kw
Width of the belt conveyer: 400mm
Length of the transportation: 5000mm
With metal detector: Chinese brand |
2 |
Compactor |
|
The movable knife in the compaction bin rotates to cut and crush the waste material entering the bin. The high-speed rotating moving knife, while crushing the material, generates frictional heat to pre-dry the waste. At the same time, with the help of a specially designed temperature control and speed control system, the heat-absorbing waste is pre-processed below the melting point temperature. shrink. The pre-shrunk waste is compacted by the guide groove inside the silo wall, and forced into the extruder feeding barrel by the centrifugal force of the rotating knife. Through this integrated process of crushing, drying and compacting, the stability and high efficiency of feeding waste with low bulk density are ensured.
Motor power:37kw
Temperature control
Way of cooling: water cooling
Qty of rotary blades:4PCS
Qty of fixed blades:9PCS
Bearing: NSK
The parts contacted with material is stainless steel |
3 |
DJ85/33 Single screw extruder |
|
The special process section (barrel, screw) designed for different kinds of wastematerials can melt and plasticize the pre-compacted waste materials more gently.
Plastic waste will be fully melted and plasticized within the targeted design process
length of 32D to 36D.
Gearbox:high torque, low noise, Hardened teeth grinding gear box with an external cooling circulatory
Motor power: 55kw,Frequency control by inverter
Speed of screw: 0~120rpm
Material of screw and barrel: 38CrMoA1A, nitride treatment
Inner surface treatment thickness: 0.4~0.7mm,
L/D: 33:1
Diameter of screw: φ85mm
Way of cooling: force wind cooling way
Heating way: by heaters
Heating zone 6
Heating power about 48KW
Cooling method Cooling fan: 0.33KW X 5 = 1.65KW
Double Vacuum Degassing system:
Vacuum pump:2.2kw
Filtration style:water filtration.
Vacuum room: special design, double zones.
Vacuum tube:temperature and pressure resistant rubber tubes.
Efficient exhaust of volatile such as micro-molecules and moisture from melt to improve quality of granules.
Self protective system:
Over-load protection of motor.
Over-pressure protection of screw. |
4 |
Plate type Hydraulic screen changer 160 |
|
Dimensions (mm)
|
d1
|
d2
|
d3
|
d4
|
h1
|
h2
|
D1
|
D2
|
D3
|
N-M1
|
N-M2
|
L
|
W
|
H
|
Φ280
|
Φ254
|
Φ254
|
Φ280
|
6
|
6
|
Φ380
|
Φ330
|
Φ266
|
12-M24
|
8-M20
|
420
|
230
|
480
|
Filtering area |
Capacity |
Heatingpower |
Hydraulicpower |
Pressure |
Temperature |
550 cm² |
≤2200kg/h |
10.2kw |
3kw |
≤35MPa
|
≤350℃
|
|
|
Single-plate double-station screen changer:
· Ring-shaped heater for consistent and stable heating.
· Leak-free operation and fast screen shift.
· Flexible sealing device.
· Stainless screen: high precision, wear resistant and pressure resistant.
Diameter: 160mm
Motor power of hydraulic:2.2kw |
5 |
Water ring cutting system |
|
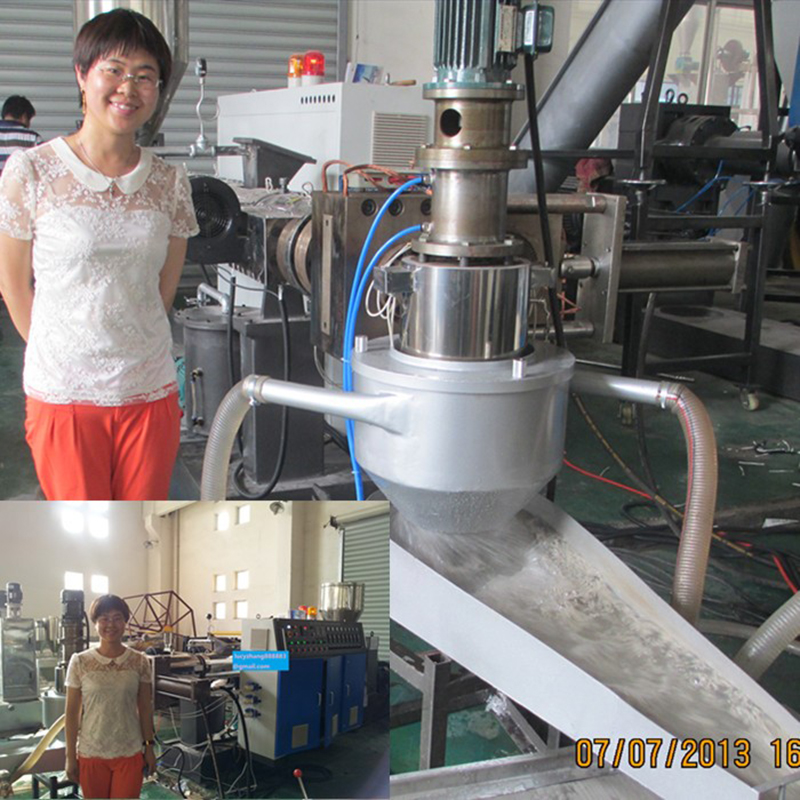 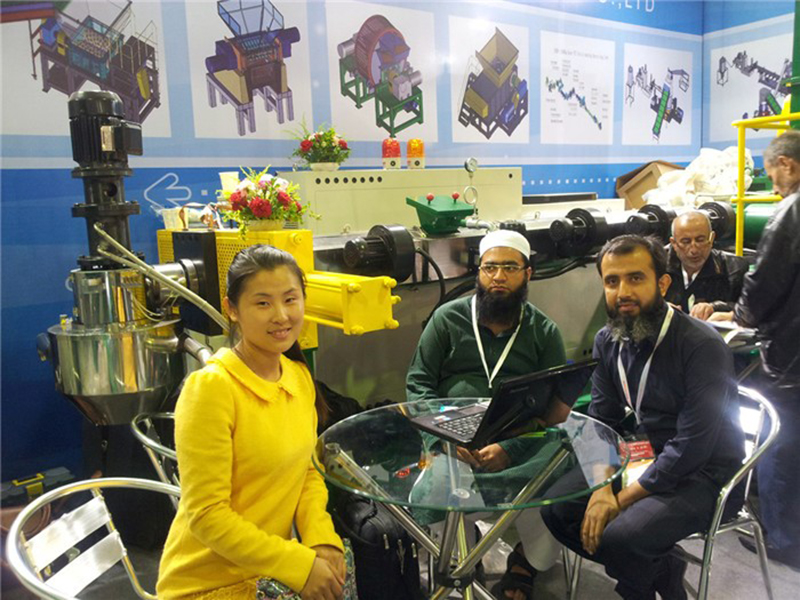 |
|
1. The speed of the pelletizing blade is automatically adjusted until the final uniform pellets appear.2. The pneumatic device is used to feed the knife to ensure good contact between the
blade and the die, and the pressure of the knife is automatically adjusted to
ensure the uniform cutting force of the knife.
Start the system with one key to make the operation of the whole system more
convenient;
Horizontal die face cutter
Power of cutter:2.2kw
Power of water pump:2.2kw
The cutter is frequency control by inverter |
6 |
Vibrating screen dewatering machine |
|
Advanced dewatering vibrating screen combined with horizontal centrifugal drying can achieve excellent drying performance and lower energy consumption.cuishi adopts a closed design and is equipped with a soundproof cover, which has low noise and is more user-friendly.
Motor power :0.25kw*2.
Parts that contact water: SUS304.
Assemble sieves: not welded. Installed and fixed by screws, for convenient replacing new sieves in the future.
Springs are surrounded with rubber, to prevent from big amplitude difference caused by spring ageing.
Special design to prevent small impurities falling into water pump.
Motor power: 3kw.
Rotary speed: 1460rpm
Parts that contact water and granules: SUS304.
|
7 |
Silo |
|
Effective capacity: 700LMaterial of the part in contact with the material Stainless steel |
8 |
Electric cabinet |
|
The control system adopts Siemens control, and is equipped with industrial-grade touch operation screen(optional item)
According to the set logical sequence and material handling process requirements, the linked cuishi system realizes one-key startup, thus avoiding mistakes in the manual startup process.
- Smart shutdown: one-key shutdown
With the help of a specially customized unit, the cuishi system can realize one-key shutdown of the entire system module to avoid equipment damage caused by incorrect operation during manual shutdown.
cuishi is equipped with an emergency stop function, which is used as an emergency for uncertain risks during the operation of the machine, shutting down the entire system promptly and quickly to avoid secondary accidents and injuries.
Life safety protection device
The cuishi system fully takes into account the safety issues of the equipment during operation. Each operating station and rotating part position are equipped with electronic safety switches to ensure the safety of the equipment during operation and avoid potential hazards during the operation of the equipment to cause harm to the customer's operators.
- Plastic performance retention
With the help of a precise temperature control system and a targeted optimization design of the plasticizing process section, the cuishi system can ensure the reliability and stability of the final pelleting quality.
- Overheating protection device for compaction chamber
With the help of modular control principle and full cognition of the performance of different recycled materials, the cuishi system can ensure that the processed waste material achieves the optimal preheating and compaction state in the compaction chamber, and can avoid the plastic return material from being compacted. Overheating or degradation in the warehouse.
Contactor: Schneider
Relay: CHNT
General switch: CHNT
Circuit-breaker: CHNT
Note: Customer need to provide the wire from control cabinet to each machine.
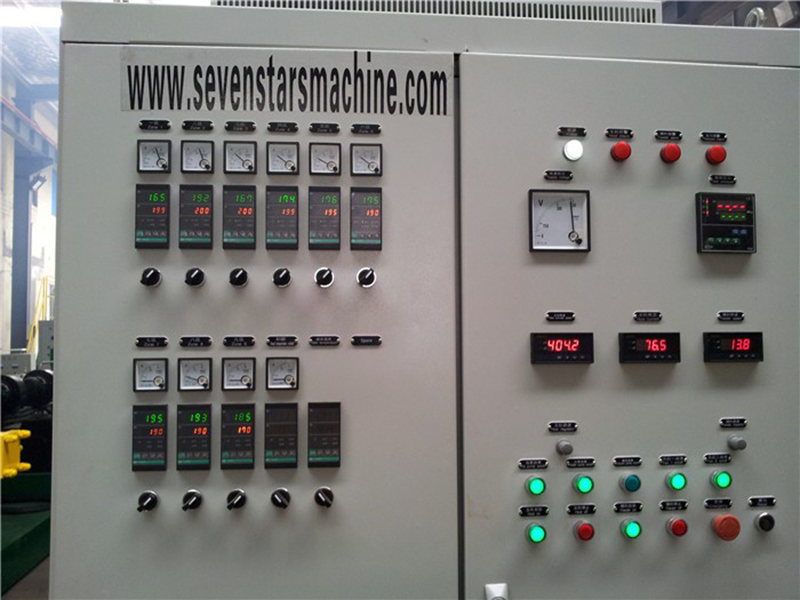
|