PET sheet production line
PET sheet line Single layer with 0.3-1mm, width 800mmh
The PET sheet production line is one of the sheet production lines with advanced technology, mature technology and stable equipment performance in our company. Calender, cooling traction bracket, double-station winding device, etc.
The equipment is compact in structure and superior in performance. The screw and barrel are optimally designed.
The whole machine has the advantages of uniform plasticization, stable extrusion, high output and long service life.
The meticulous shaping and calendering device makes the sheet well shaped through its good adjustment function.
The PET sheet produced by this equipment can be thermoformed into various packaging products, has good gas barrier properties, does not contain other additives, is pure and hygienic, has good toughness and extensibility, and excellent recyclability. , can be widely used in electrical appliances, toys, food, medicine and other packaging and the vast printing industry.
Compared with domestic similar equipment, the comprehensiveness is more than 30% higher. This production line can also be used for PS, PP, PE and other sheet products.
The pet sheet line including the feedings, extruders ,melt lines ( including filtration, metering)dies , casting sheets , traction and winding.
Design basic data
Features of PET sheet production line equipment:
1. The special screw design increases the unit production capacity while ensuring the mixing and high plasticizing capacity, with a production capacity of 1.5 tons/hour.
2. The double-throttle design of the inner-blocking hanger-type die head can be used to adjust the width of the product online on the premise of ensuring the uniformity of thickness.
3.The real-time control system of imported electrical components ensures the stability and reliability of the system.
4. Three-roller calender with spiral inner flow channel, the inner wall is CNC car-washed, and the temperature is guaranteed to be controlled within ±1°C.
5. Using Siemens PLC, the whole system is automatically controlled without manual adjustment.
6. Fully automatic double station winder, controlled by servo motor, fast speed 60m/min
7. Raw materials: polyester pure raw materials, or polyester recycled materials:
PET type: raw material slice,
φ 3mm*L3mm ,Bulk density: 700~880kg/m3
2.3 polyester recycling material type:
PET bottle, PET chip recycling material, diameter 3mm- diameter 6mm,Thickness ≥ 0.15mm,Intrinsic viscosity: 0.5~0.65g/dl
Moisture content: ≤ 0.5 ‰
8. product characteristics:Thickness: 0.3-1.0mm
Structure: single layer, layer proportion: 100%
Width: 800mm (after trimming)
Winding diameter (maximum): 600mm (mechanical design limit)
production speed: 3~30m/min
extrusion capacity:Design capacity: 450kg/h
Technical specification
Part 1 :Twin screw host/extruder 75/132kw 40:1
Drying and mixing of raw materials 2m3 dry mixing hopper
Feeding system :Spiral feeding
feeding system: Volumetric metering feed
Cooling system :Air cooling
Forced vacuum pumping system :Water ring vacuum pump + buffer tank
Reduction gearbox :High torque reduction gearbox NSK bearing
Production line steel frame platform :Including screen changer support, melt pump and die hanger
Part 2 :screen changer, metering pump and T shape mould
Part 3:three calender unit with diameter 400 500 500mm
Independent drive calender can be adjusted from front to back, up and down
Hauling off unit :Aluminum idler
Traction of one rubber roller and one steel roller 160mm motor 1.5kw
Automatic synchronization with tension adjustment
ABB frequency converter
Italian Jefferson displacement sensor
Part 4Part 4 :tractor /sheet hauling off 1 set cut edge unit : with knife 2 pcs
Part 5: double position winder 1 set
Part 6 electrical parts
It includes temperature control part and adopts solid-state relay. Drive control part, variable frequency motor, Siemens PLC, Taiwan vellon touch screen. The speed control and pressure closed-loop control are realized for the transmission device of the extruder. Perfect alarm, protection, and historical records at all levels to facilitate production and control.
Ⅲ. Detailed description of the production line
Part I: twin screw extruder
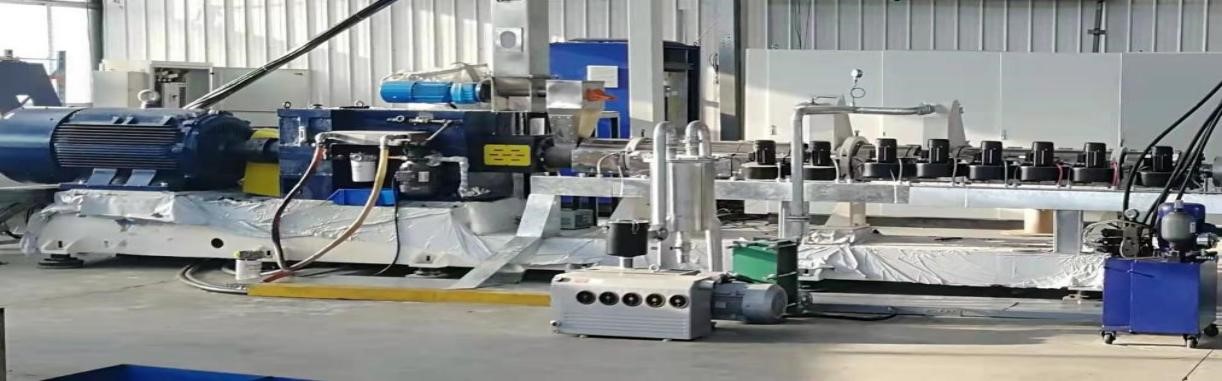
1. raw material mixing and feeding system 1 set
Equipped with dry mixing hopper, with a volume of 2 cubic meters
Spring coil feeding.Stainless steel outer tube, spring made of high-quality spring steel. The material can be automatically replenished through the material level sensor.
1.0) screw metering feeder
Installed at the first barrel 1 set
Screw metering feeding, motor power: 1.5kw
The speed regulation mode is controlled by AC frequency converter
2.0) twin screw extruder 1 set
2.1) One Drive motor:Adopt variable frequency motor, with power of 132kw; Governor:Select frequency converter;
Screw speed:30--300rpm; Power transmission:Coupling
Gearbox:High torque reducer.
Speed reduction and torque distribution are integrated to strengthen the design of bearing capacity;
The gear is made of high-quality alloy steel. After carburizing and quenching, the gear is precisely ground. The machining accuracy is above grade 5. The tooth surface hardness reaches hrc60-65. The tooth profile and helix are modified to ensure the perfect engagement of the gear under load, with low noise and large transmission torque;
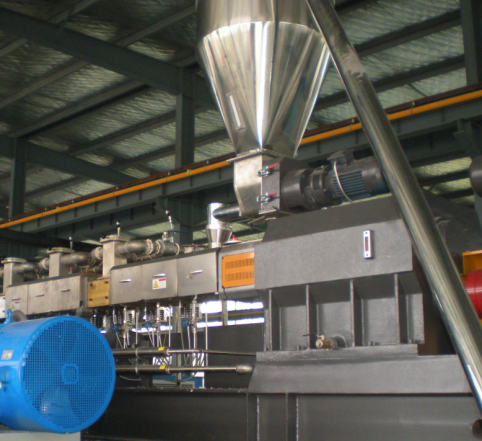
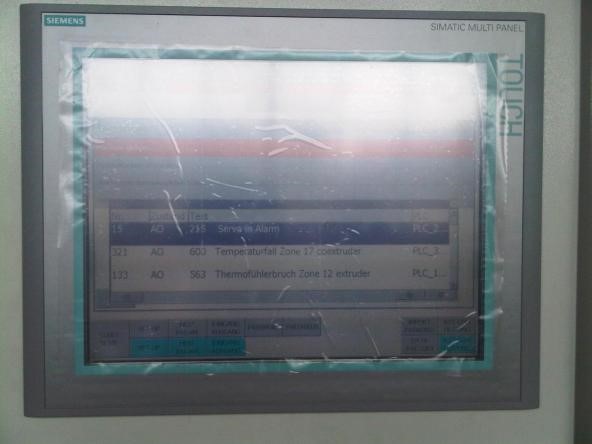
The oil lubrication system mainly adopts oil immersion lubrication and multi-point spray lubrication to ensure that all moving pairs are always lubricated;
New designed sealing structure and imported brand sealing ring ensure excellent sealing performance of input and output shafts;
Lubricating oil cooling: plate heat exchanger, circulating water cooling; Lubricating oil pump: built-in;
Twin screw extrusion system: screw element:
The diameter of the screw is ¢ 75mm, which is connected with the mandrel by advanced involute spline; Computer optimized design, precision machining, excellent self-cleaning and interchangeability;
According to the processing materials and processing technology, and with the help of years of rich experience in screw configuration R & D and design and software advantages, the building block combination can efficiently realize the functions of conveying plasticization, mixing and mixing, shear dispersion, homogenization, exhaust devolatilization, pressure building extrusion and so on.
Component material: high quality 38CrMoAlA nitriding steel after 72 hours nitriding treatment; Screw rotation direction: rotate in the same direction.
Material: made of high-strength alloy steel high-strength quenching and tempering treatment, hardness 300-350hb, composite forging, improve strength and toughness, and ensure the transmission requirements of screw torque.
Cylinder:The cylinder adopts modular design, which can be freely combined, precision machined and excellent interchangeability. Barrel material: high quality 38CrMoAlA nitriding steel after 72 hours nitriding treatment;
Barrel heating: electric heating, cast copper and cast aluminum heaters are used, and the heating temperature
Barrel cooling: fan cooling is adopted, with low energy consumption and small temperature difference change, which is conducive to pet processing. Connection middle body:
Cast steel material, precision machining, effectively ensuring the straightness between the transmission case and the cylinder and the coaxiality of the transmission case output shaft and screw.
Cylinder support:
Double support structure, stable operation;
An axial displacement pressing mechanism is designed between the cylinder support and the cylinder to eliminate the deformation and vibration of the extruder due to the thermal expansion of the cylinder.
Cylinder connecting bolts:
grade heat-resistant and high-strength bolts shall be used for connecting the cylinder
Base:The base is rigid and equipped with special machine tool damping pad, which has low vibration, low noise, stable operation and no special foundation.
Cylinder cover:The split type stainless steel insulation cover of each section of the main engine cylinder is lined with insulation materials, which is beautiful and convenient, improves the equipment insulation effect, reduces energy consumption, reduces the external surface temperature of the cylinder, and prevents scalding.
vacuum pumping system
vacuum pump: water ring vacuum pump + roots pump
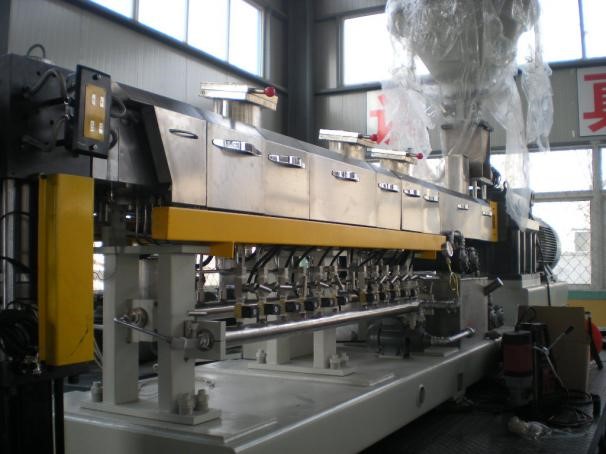
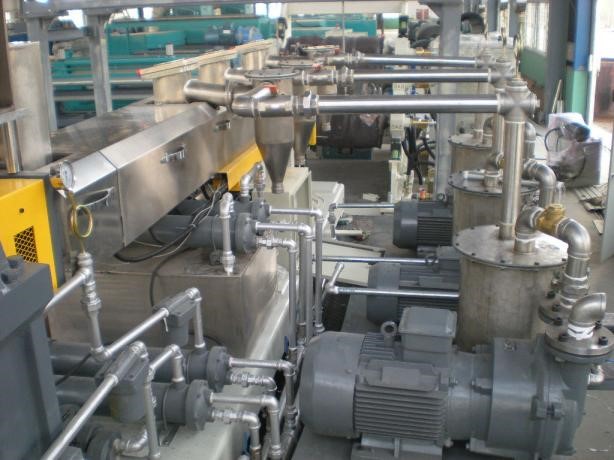
Vacuum condensing tank: stainless steel vacuum condensing separation tank, equipped with tower plate filter water grid to facilitate the filtration of impurities and volatiles.
The two-stage structure of vacuum condensing tank can automatically control the removal of water, volatile matter and waste. The vacuum degree can be hardly affected during the removal process.
High pressure rubber hose is used, which is easy to disassemble and can play the role of heat preservation.
Each vacuum zone is equipped with an independent vacuum system, which has a high degree of freedom and does not interfere with each other. Problems in one zone will not affect the whole system.
The unique overflow port design enables pet to emerge from the port without flowing into the vacuum pipe in case of material emission. Convenient for disassembly and cleaning.
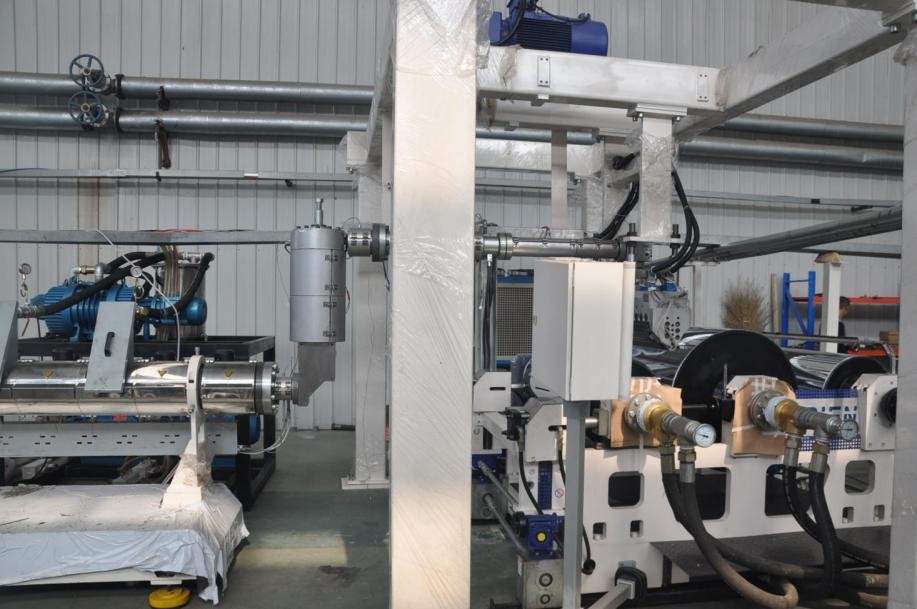
2.3 transition connector 1 piece
High quality nitriding steel (38CrMoAlA) materia
nitriding treatment, equipped with pressure sensor hole
Part II:screen changer and metering pumpn and T shape mould
double column screen changer 1 set
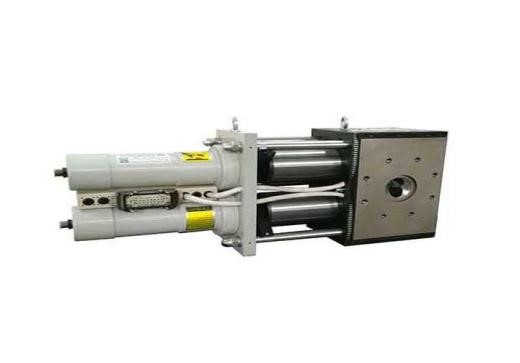
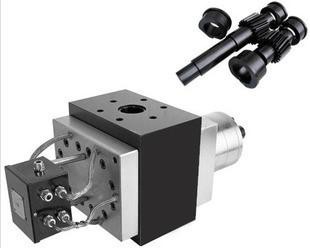
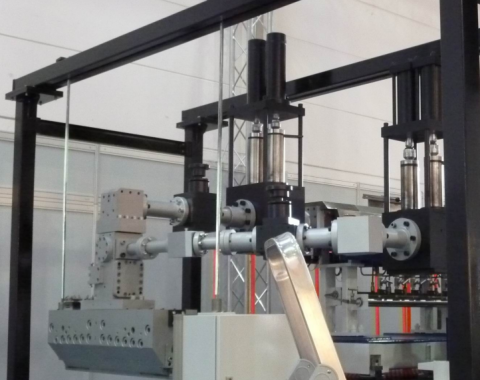
metering pump 1 set characteristic
all reducers adopt Dongli reducers to ensure transmission accuracy.
pressure sensor and melt pipe
characteristic
sensor is used for pressure acquisition in front of the pump.
through the control system, the pressure sensor is used for closed-loop control of the extruder, which can automatically adjust the extruder speed and blanking volume, so as to ensure the stability of extrusion pressure.
T-shaped mold 1 set
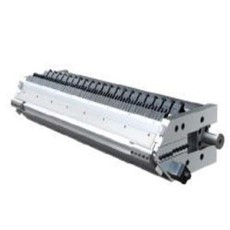
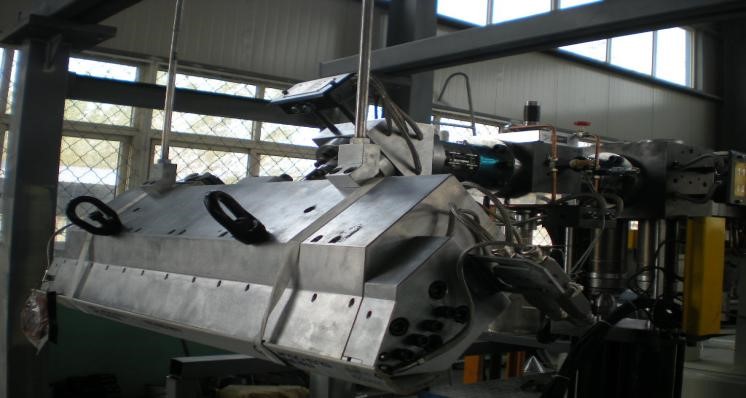
characteristic
chrome plating and polishing. Hardness greater than HRC 55
layer proportion: single layer
Product width mm eight hundred and eighty
Part 3:three calender unit with diameter
1. three roll calender1 set
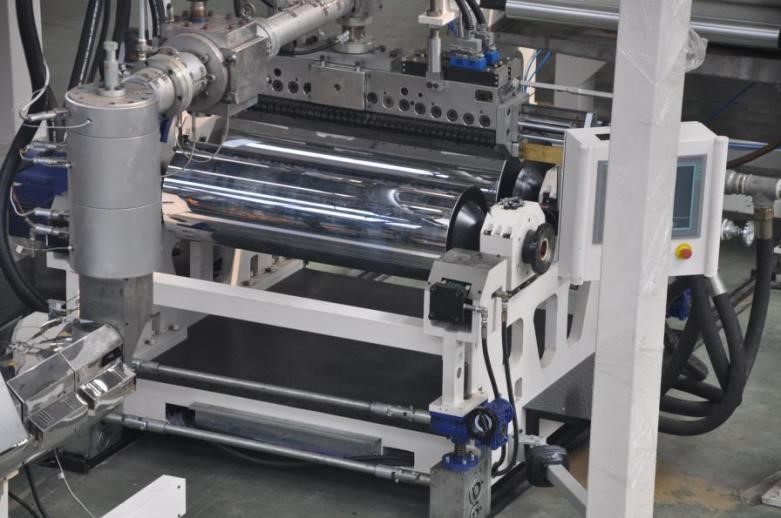
characteristic
rope pulling emergency stop device and Schneider emergency stop switch.
roller clamping and separation: the hydraulic cylinder is adjusted, and the sliding adopts linear guide rail.
the hydraulic station adopts automatic pressure maintaining design, with a maximum pressure of 8Mpa.
temperature regulating roller: water cascade cooling, using water chiller to cool the water, (water chiller needs Optional)
roller gap adjustment servo motor control, which can be set with one key in the control system. (additional options required)
the calender can be adjusted up and down, front and back.
Product width mm eight hundred and eighty
Product thickness Min. min mm zero point five
Max. max mm one point two
Reducer Independent drive Dongli reducer
Drive motor Variable frequency motor kw two point nine
Mobile motor power kw zero point seven five
Part 4 :tractor /sheet hauling off 1 set
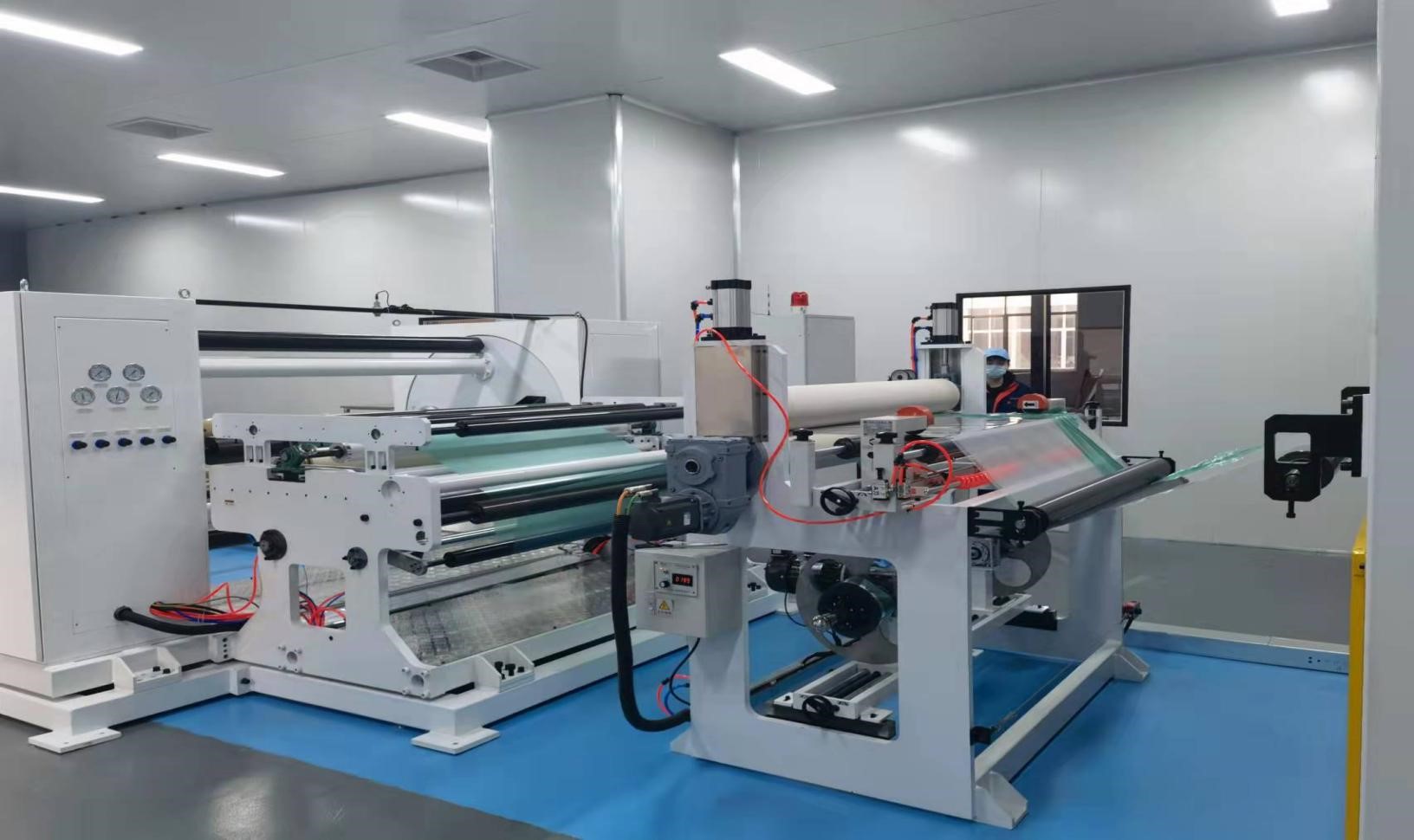
characteristic
upper roll rubber roll, lower roll steel roll traction
tension control is realized between traction and three rollers, and also between traction and winding. When the whole machine speeds up and different sheet thicknesses are produced, manual control is not required, and the speed can be increased at the same time to make the equipment operate normally. Italian Jefferson displacement sensor is adopted.
push button emergency stop device
with trimming system. It is also equipped with two waste edge winding equipment.
Reducer :Dongli brand
1. winder 1 set characteristic
Moment winding
Dual/double position station
servo motor control
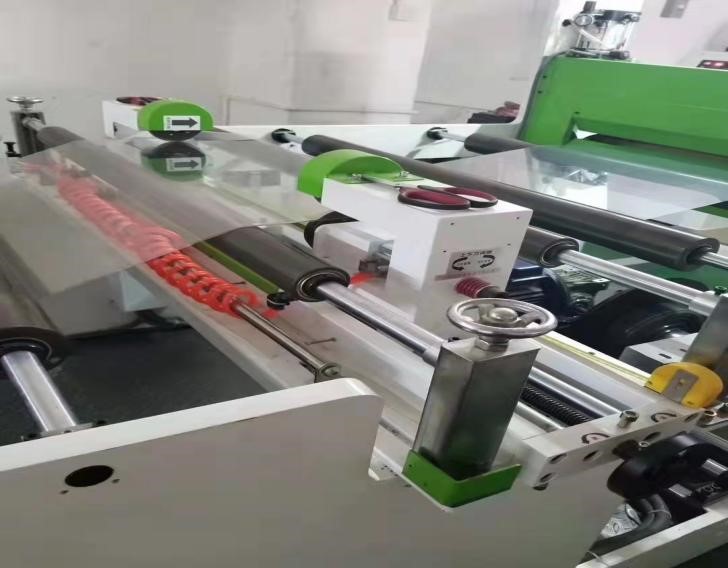
Trimming unit. Edge material recovery
With trimming system. And equipped with two waste edge winding equipment.
Round knife cutting.
Torque motor collects waste edge
Automatic film storage machine
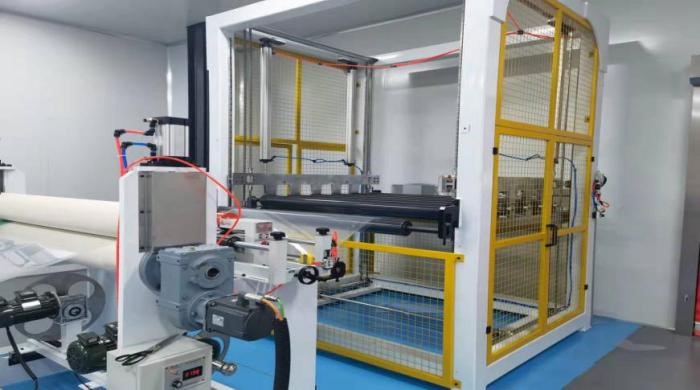
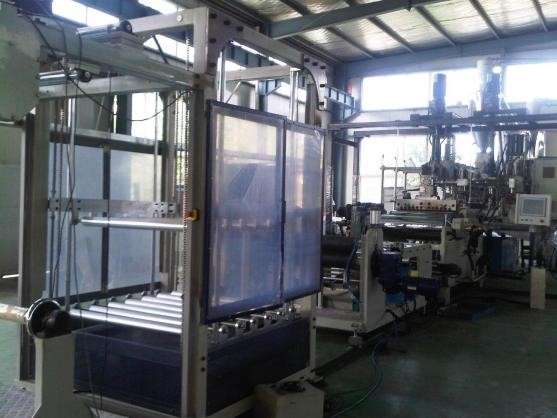
during automatic roll change
Aluminum guide roller: φ=76mm, L=1100mm surface brown oxidation treatment.
Can store 16m sheets;
Part 5: double position winder 1 set
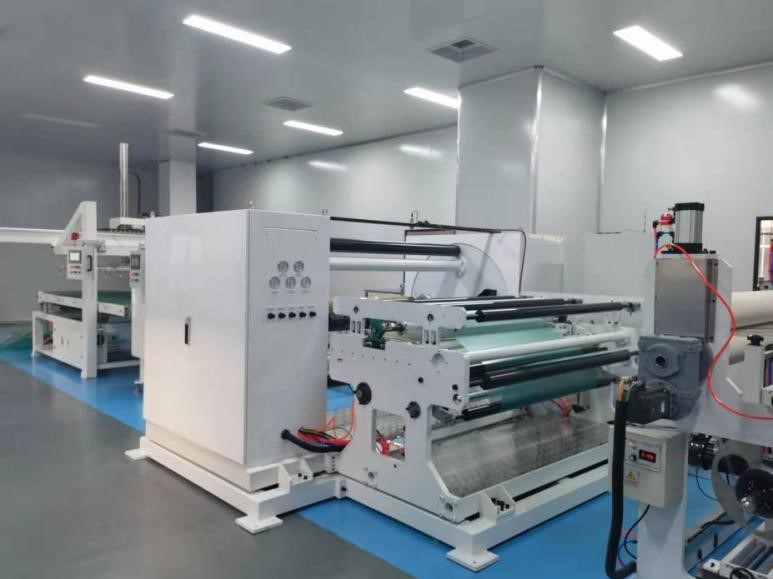
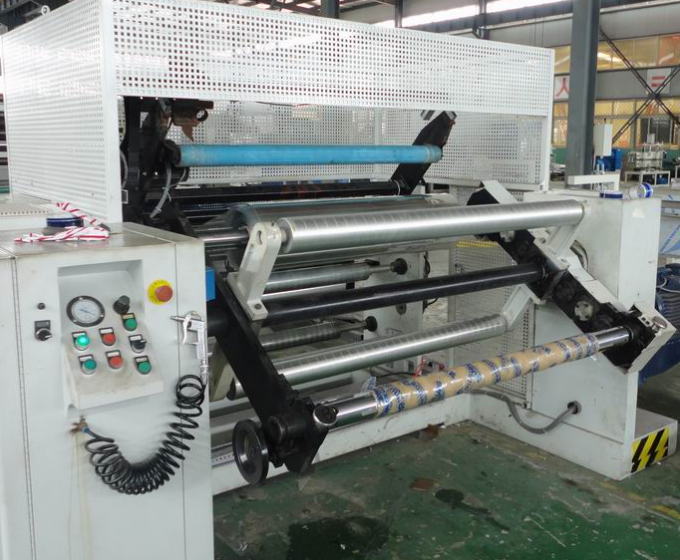
Winding structure: turret center, gap winding mode;
Rewinding function: It has two functions of contact rewinding and gap rewinding;
PART 6 electric drive system
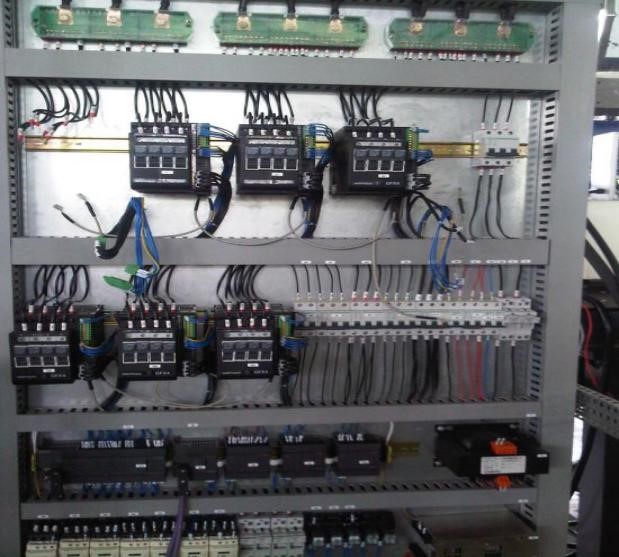
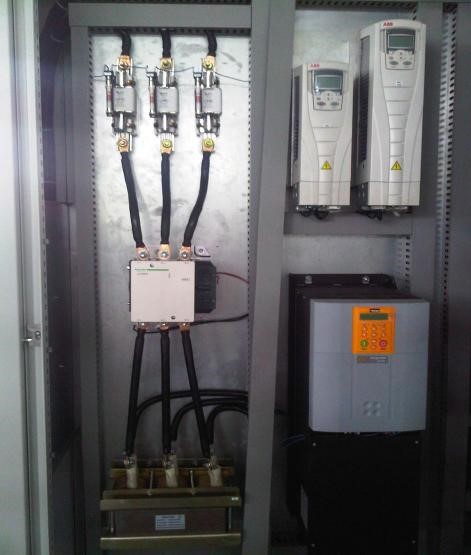
Pet electric drive system is used to provide driving devices for various pet divisions, including main extrusion unit, cooling roller, traction unit and turnover double position winder.
When the encoder feedback is adopted for the transmission device, the speed stability accuracy can reach 0.1%. Speed control and pressure control shall be realized for the transmission device of the extruder. High transmission accuracy is required for the main extruder and cooling roller,
to ensure the uniformity of longitudinal tolerance of PET sheet. Floating rolls or tension sensors are used for speed coordination between the three roll calender and the tractor.
the speed setting from the cooling roller to the traction unit is in a speed chain relationship to ensure that the linear speed of the production line is coordinated, and the linear speed of the production line can be given by the cooling roller according to the product specification, and can be set arbitrarily.
Part 7 On line sheet handling equipment and other auxiliary equipment
1..On line silicone oil coating system and. Silicone oil coated with 2m oven
Waste edge online recovery system 2 sets
2. Three roll calendering heat exchange
3. Water heating and cooling ( provided by chiller)
heat exchange characteristics of three roll rolling
4. pet recycling material crystal system
5. 30HP Air cooled chiller
1. inline silicone oil coating system and. Silicone oil coated with 2m oven
Waste edge online recovery system 2 sets
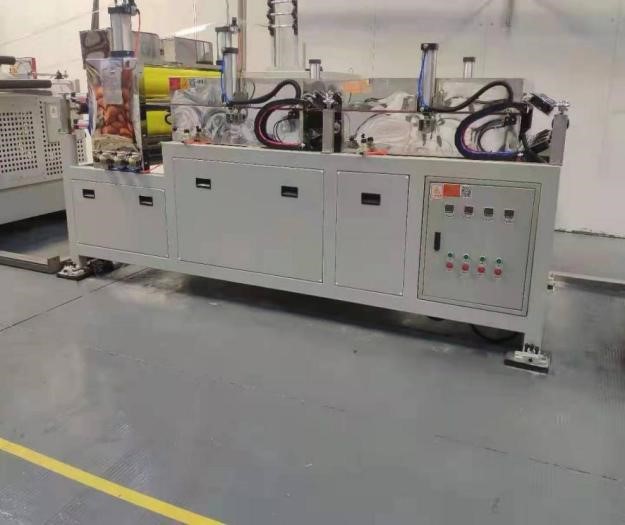
With 2m oven ,One side coated with silicone oil
4. pet recycling material crystal system
5, 30HP Air cooled chiller
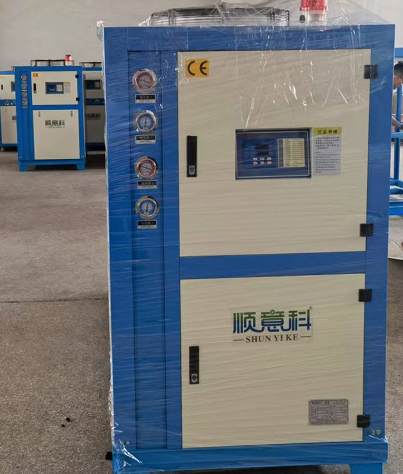

PARAMETER MODEL |
SYF-30 |
|
|
|
Refrigerating capacity |
Kw 50Hz/60Hz |
92.6 |
|
|
110.66 |
|
|
||
Power supply and electrical components |
380v 50HZ |
|
|
|
Refrigerant |
Name |
R22 |
|
|
The control mode |
Internalbalance expansion valve |
|
|
|
The compressor |
Type |
Closed vortex type |
|
|
Power(Kw) |
27.4 |
|
|
|
The condenser |
Type |
High efficiency copper clad aluminum fins +low noise external rotor fan |
|
|
Fan power and quantity |
0.75Kw*3 |
|
|
|
Cooling air volume(m³/h) |
28290 |
|
|
|
The evaporator |
Type |
Water tank coil type |
|
|
Frozen water volume(m³/h) |
22.07 |
|
|
|
26.48 |
|
|
||
Tank capacity(L) |
580 |
|
|
|
Water pump |
Power(Kw) |
3 |
|
|
Lift(m) |
40 |
|
|
|
Flow rate(m³) |
25 |
|
|
|
Pipe diameter interface |
DN65 |
|
|
|
Security and protectio |
Compressor overheat protection, overcurrent protection, high and low pressure protection,overtemperature protection, phase sequence/phase protection, exhaust overheat protection. |
|
|
|
Mechanical dimensions |
Long(mm) |
2500 |
|
|
Width(mm) |
1000 |
|
|
|
High(mm) |
1700 |
|
|
|
Input total power |
KW |
34.5 |
|
|
Mechanical weight |
KG |
1100 |
|
|
Note:1.The refrigerating capacity is based on:freezing water inlet and outlet water temperature 7℃/12℃,cooling inlet and outlet wind temperature 30℃/35℃. | ||||
2.Scope of work:frozen water temperature range: 5℃to35℃;Freezing water inlet and outlet temperature difference: 3℃to8℃,The ambient temperature is not higher than 35℃. | ||||
Reserves the right to change the above parameters or dimensions without notice. |
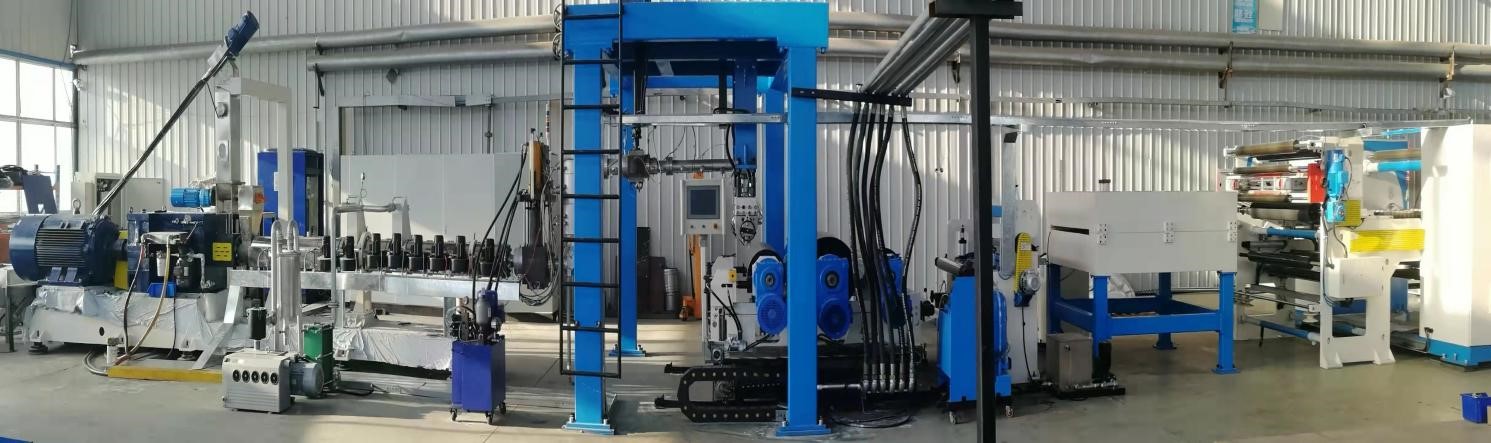