plastic pe pipe line
QINGDAO CUISHI PLASTIC MACHNERY CO.,.LTD was established in 1999. The production experience is mature and rich. Among them, it has been exporting for more than 24years. Our company's production base covers more than 30,000 square meters., with experienced high-quality staff team, first-class equipment, perfect and effective quality assurance system, advanced and complete testing equipment.
PE Pipe Extrusion Line.
20mm 110mm 315mm 630mm 800mm 1200mm 1600mm plastic pe pipe extruder making production line/machine
315mm LDPE HDPE PE pipe making machine/production line /extruder machine for water and gas
Customized 315mm PE HDPE LDPE Pipe Making Machine Plastic Pipe Extrusion Production Line

Through long time and continuous innovation and testing, qingdao cuishi has developed the new generation PE pipe extrusion line with high automation, high speed, high reliability, low energy consumption. Our PE pipe extrusion can process wide range of material, including HDPE, LDPE, PP, PPR, PPH, PPB, MPP, PERT, etc.
Our PE pipe extrusion line can produce from size of minimum 16mm to 2000mm with single layer or multi-layer.
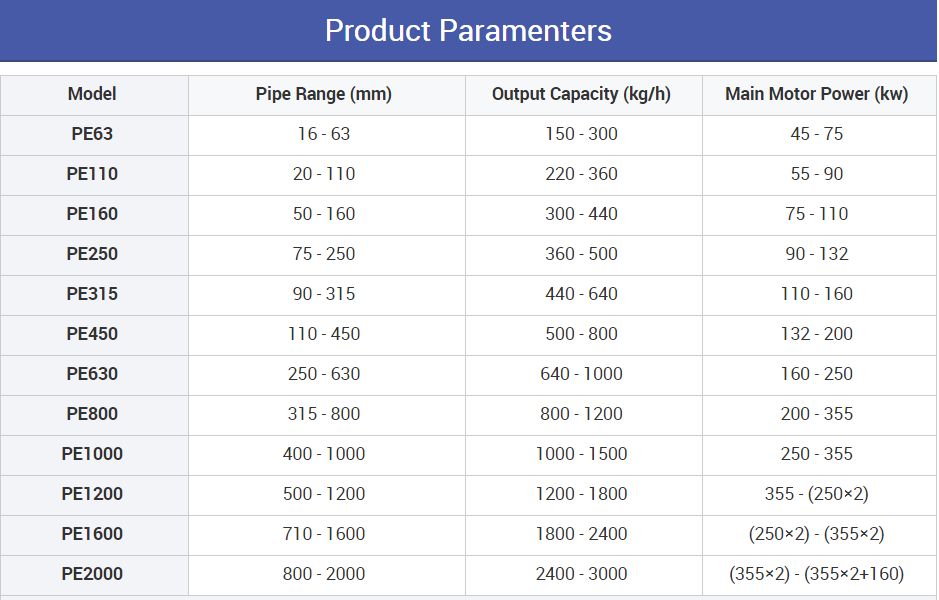
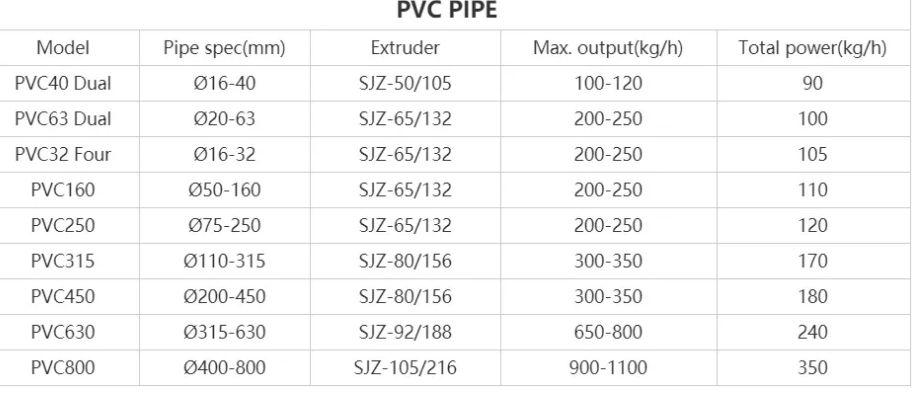
1.Single Screw Extruder.
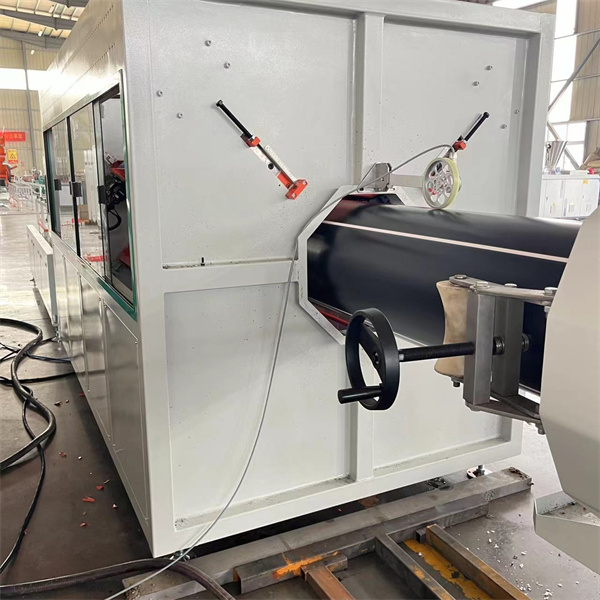
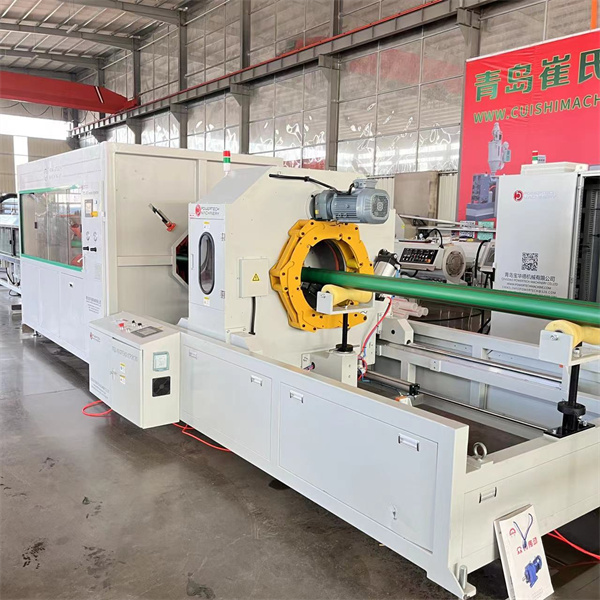
1.1Simens Touch Screen and PLC
1.2 Spiral Structure of Barrel
1.3 Special Design of Screw
1.4 Air Cooled Ceramic Heater
1.5 High Quality Gearbox
Based on 38:1 L/D ratio for screw design, we have developed 38:1 L/D ratio. Compared with 33:1 ratio, 38:1 ratio has advantage of 100% plasticization, increase output capacity by 30%, reduce power consumption up to 30% and reach almost linear extrusion performance
2.Extrusion Die Head.
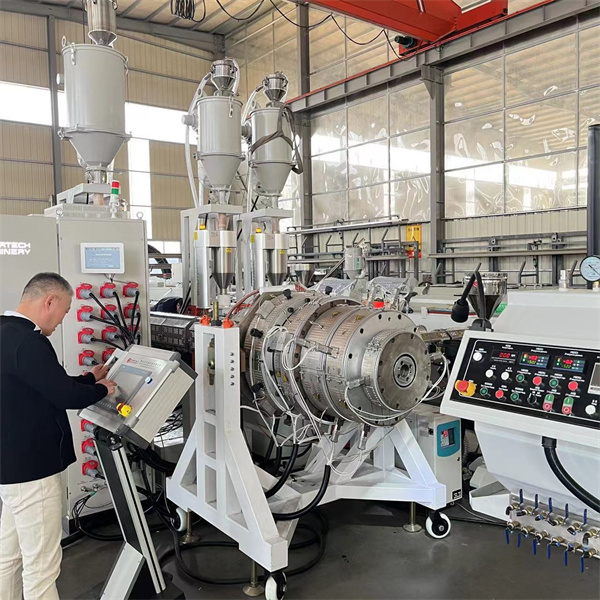
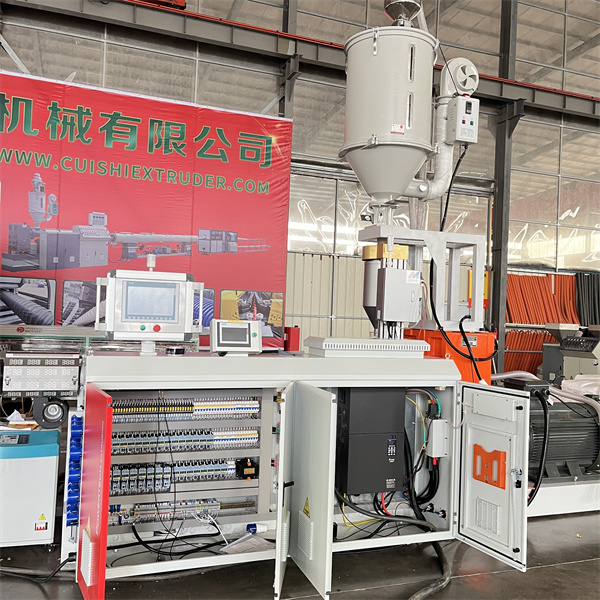
2.1 Moving Device of Die Head
2.2 Die Head Rotary Device
2.3 Heat Exhausting Device
2.4 Cooling Device for Core
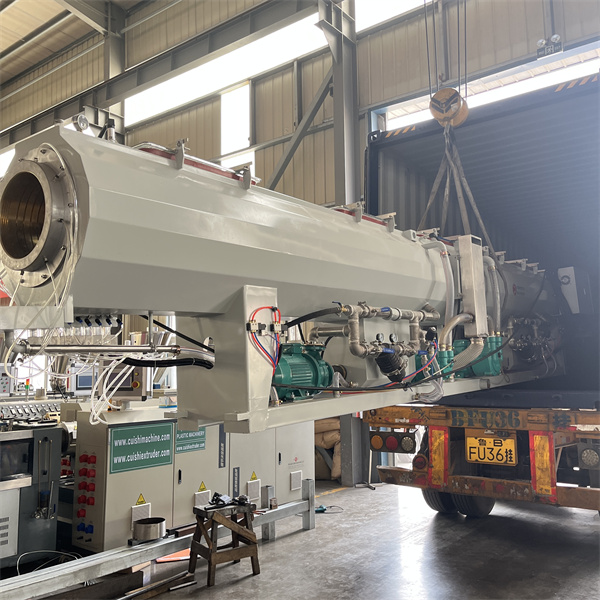
2.1Extrusion die head apply spiral structure, each material flow channel is placed evenly. Each channel is after heat treatment and mirror polishing to ensure material flow smoothly. Die head structure is compact and also provide stable pressure, always from 19 to 20Mpa. Under this pressure, pipe quality is good and very little effect on the output capacity. Can produce single layer or multi-layer pipe.
3.Vacuum Tank.
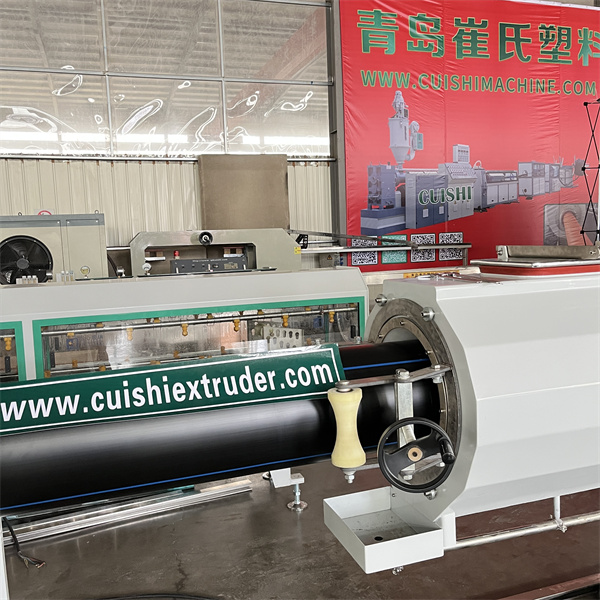
3.1 Strong Cooling for Calibrator
3.2 Better Support for Pipe
3.3 Silencer
3.4 Pressure Relief Valve
Vacuum tank is used to shape and cool pipe, so as to reach standard pipe size. We use double-chamber structure. First chamber is in short length, to ensure very strong cooling and vacuum function. As calibrator is placed in the front of first chamber and pipe shape is formed mainly by calibrator, this design can ensure quick and better forming and cooling of pipe.
4.Cooling Tank.
4.1 Pipe Clamping Device
4.2 Water Tank Filter
4.3 Quality Spray Nozzle
4.4 Pipe Support Adjusting Device
4.5 Pipe Support Device
Cooling tank is used to cool pipe further.
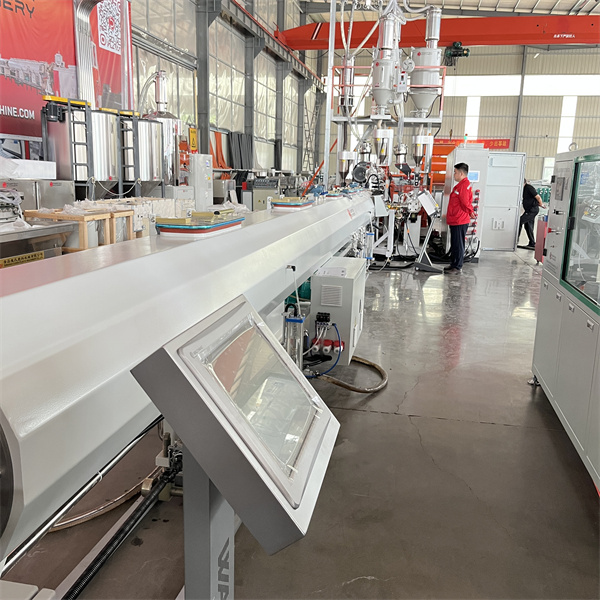
5Haul off unit.
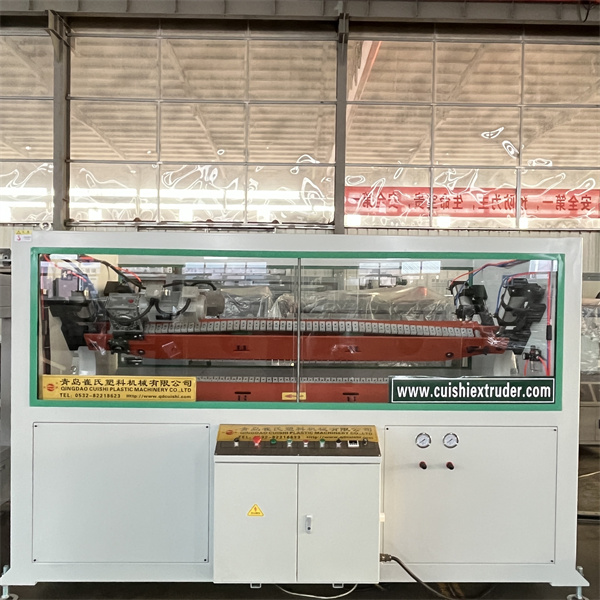
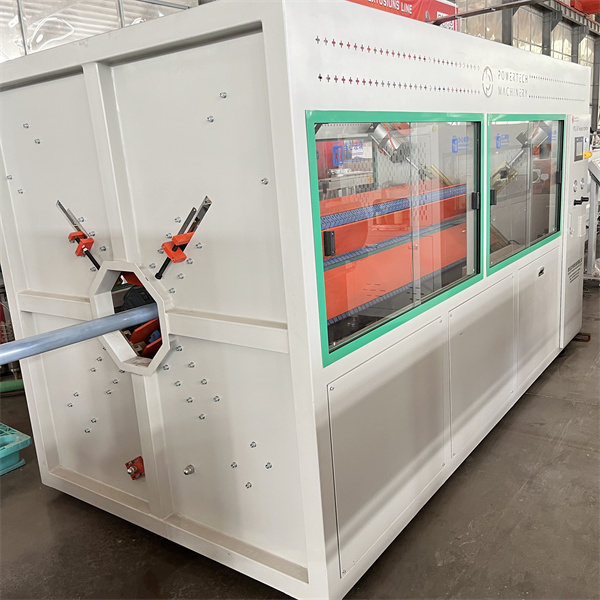
5.1 Pipe Clamping Device
5.2 Water Tank Filter
5.3 Quality Spray Nozzle
5.4 Pipe Support Adjusting Device
5.5 Pipe Support Device
5.6 FOUR CATERPILLER PIPE HAULING OFF
Haul off unit provides sufficient traction force to pull pipe stably. According to different pipe sizes and thickness, our company will customize traction speed, number of claws,effective traction length. To ensure match pipe extrusion speed and forming speed, also avoid deformation of pipe during traction.
6.CUTTER

6.1 Universal Clamping Device
6.2 Central Height Adjustment
6.3 Saw and Blade Interchangeable FOR 110-315MM NON DUST CUTTER
Cutter controlled by Siemens PLC, working together with haul off unit to have precise cutting. Customer can set the length of pipe
they want to cut. Multi-feed-in actions for the accomplishment of one cutting process (protect blades and saws, prevent from blade
and saws stuck for thick pipe and cut face of pipe is smooth).
WINDER CAN COIL 110MM
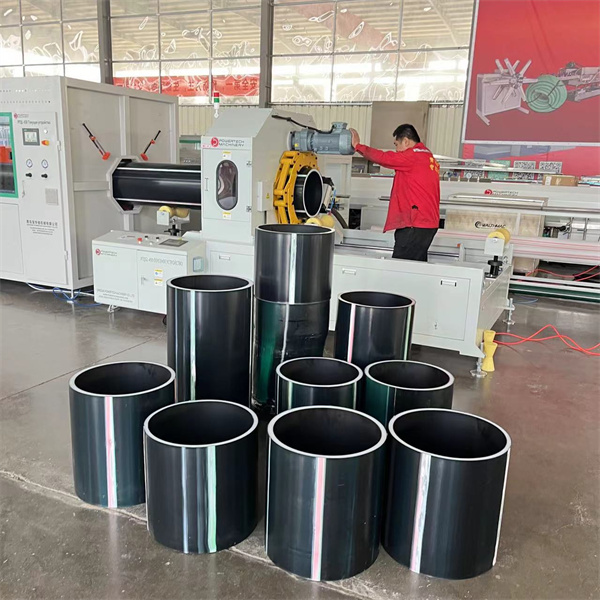
